KO TECHNOLOGIES- CUSTOM DRIVE TRAIN AND BRUSHLESS MOTOR DESIGN.


ACTIVE CHOKE POINT TECHNOLOGY
THE ULTIMATE MOTOR DESIGN AND MANUFACTURING TECHNOOGY

DELIVERING UNMATCHED BRUSHLESS MOTOR TECHNOLOGY TO ANY APPLICATION
Our motors boast a whole range of technical achievements and industry firsts
CRYO TECHNOLOGY - RACE OIL X - ACPC - OPEN CAGE BEARINGS - REMOVABLE BASE PLATE - WET SUMP
The traditional fan or fin styled design calls for a fan machined in to the bell. Either on the inside or outside of the motor. This method has 2 major flaws.
Firstly this design is" handed " meaning clock wise rotating motors must have a fan design orientated differently to a counter clock wise rotating motor if the fan is to be effective.
Second is the fact that a fan, or fan shaped spokes design robs the motor of power to drive the fan. In turn lowering response times, ultimate RPM and ultimate available torque.
KO Technologies is the very first motor company to incorporate a cooling system into radio control brushless motors that does not rely on fans or fin style designs .
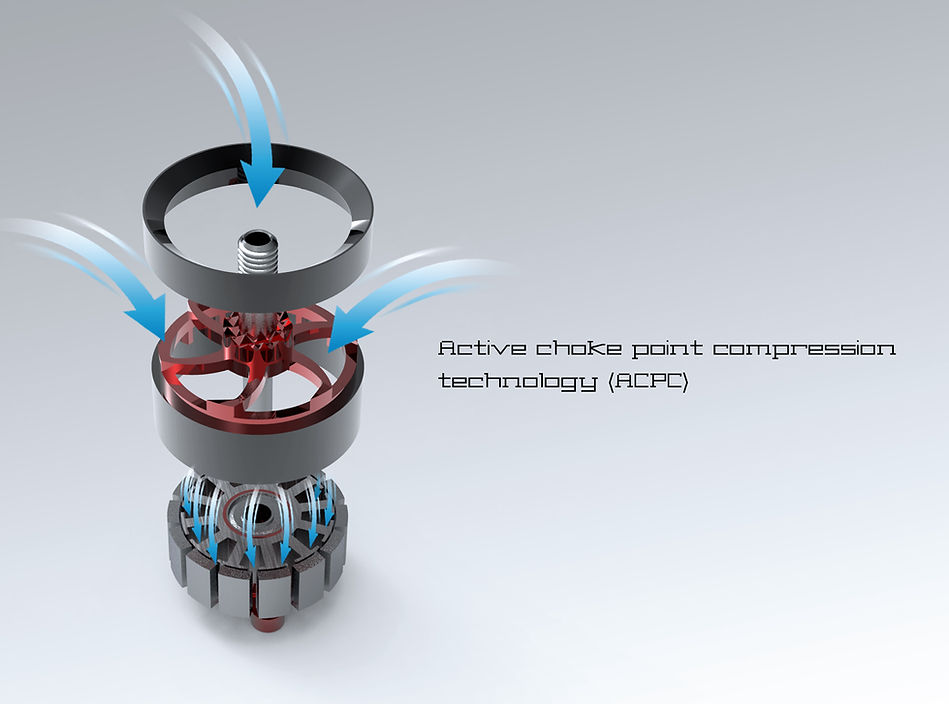
THE BENEFITS OF ACTIVE CHOKE POINT TECHNOLOGY
KO Technologies has developed ACPC to compress oncoming air directly at the bell spoke face. This forces the air past the spokes and directly into the stator and magnet assembly. This in turn lowers the temperature, increases torque and dramatically increases response times all the way along the rpm range. As a bonus the angled ring that forms the ACPC design is used as a counter balance used to reduce the amount of putty used to balance a motor bell.
​
We are able to "clock" the ACPC ring a full 360 ° during the balance procedure, effectively halving the amount of putty needed to achieve a reading of "True" on the test equipment . This allows us to further reduce the bells weight and in turn improve motor response times. Lastly because of this ability to reduce the amount of balance putty putty needed. We have also been able to reduce the lip at the base of the motor used as a rebate to retain the putty under high RPM centrifugal forces, further reducing weight and I'm proving response times.